പ്ലൈവുഡ് മൂന്നോ അതിലധികമോ നേർത്ത തടി പാളികൾ ഒരു പശ ഉപയോഗിച്ച് ബന്ധിപ്പിച്ചാണ് നിർമ്മിച്ചിരിക്കുന്നത്. മരത്തിന്റെ ഓരോ പാളിയും അല്ലെങ്കിൽ പ്ലൈയും സാധാരണയായി അതിന്റെ ധാന്യം തൊട്ടടുത്ത പാളിയിലേക്ക് ലംബ കോണുകളിൽ ഓടുന്ന രീതിയിൽ ക്രമീകരിക്കപ്പെടുന്നു, ഇത് ചുരുങ്ങൽ കുറയ്ക്കുന്നതിനും പൂർത്തിയായ ഭാഗത്തിന്റെ ശക്തി മെച്ചപ്പെടുത്തുന്നതിനും സഹായിക്കുന്നു. മിക്ക പ്ലൈവുഡും കെട്ടിട നിർമ്മാണത്തിൽ ഉപയോഗിക്കുന്ന വലിയ, പരന്ന ഷീറ്റുകളിലേക്ക് അമർത്തുന്നു. മറ്റ് പ്ലൈവുഡ് കഷണങ്ങൾ ഫർണിച്ചറുകൾ, ബോട്ടുകൾ, വിമാനങ്ങൾ എന്നിവയിൽ ഉപയോഗിക്കുന്നതിന് ലളിതമോ സംയുക്തമോ ആയ വളവുകളായി രൂപപ്പെടുത്താം.
ബിസി 1500-ൽ, ഈജിപ്ഷ്യൻ കരകൗശല വിദഗ്ധർ ടുട്ട്-അങ്ക്-അമോൻ രാജാവിന്റെ ശവകുടീരത്തിൽ നിന്ന് കണ്ടെത്തിയ ഒരു ദേവദാരു പെട്ടിയുടെ പുറംഭാഗത്ത് ഇരുണ്ട എബോണി മരത്തിന്റെ നേർത്ത കഷണങ്ങൾ ബന്ധിപ്പിച്ചപ്പോഴാണ് നിർമ്മാണത്തിനായി തടിയുടെ നേർത്ത പാളികൾ ഉപയോഗിച്ചത്. പിന്നീട് ഗ്രീക്കുകാരും റോമാക്കാരും മികച്ച ഫർണിച്ചറുകളും മറ്റ് അലങ്കാര വസ്തുക്കളും നിർമ്മിക്കാൻ ഈ സാങ്കേതികവിദ്യ ഉപയോഗിച്ചു. 1600-കളിൽ, നേർത്ത മരക്കഷണങ്ങൾ കൊണ്ട് ഫർണിച്ചറുകൾ അലങ്കരിക്കുന്ന കല വെനീറിംഗ് എന്നറിയപ്പെടുന്നു, കൂടാതെ കഷണങ്ങൾ തന്നെ വെനീറുകൾ എന്നറിയപ്പെടുന്നു.
1700-കളുടെ അവസാനം വരെ, വെനീറിന്റെ കഷണങ്ങൾ പൂർണ്ണമായും കൈകൊണ്ട് മുറിച്ചിരുന്നു. 1797-ൽ, ഇംഗ്ലീഷുകാരനായ സർ സാമുവൽ ബെന്താം വെനീറുകൾ നിർമ്മിക്കുന്നതിനുള്ള നിരവധി യന്ത്രങ്ങൾ ഉൾക്കൊള്ളുന്ന പേറ്റന്റുകൾക്ക് അപേക്ഷിച്ചു. തന്റെ പേറ്റന്റ് അപേക്ഷകളിൽ, കട്ടിയുള്ള ഒരു കഷണം രൂപപ്പെടുത്തുന്നതിന് പശ ഉപയോഗിച്ച് വെനീറിന്റെ നിരവധി പാളികൾ ലാമിനേറ്റ് ചെയ്യുന്ന ആശയം അദ്ദേഹം വിവരിച്ചു - ഇപ്പോൾ നമ്മൾ പ്ലൈവുഡ് എന്ന് വിളിക്കുന്നതിന്റെ ആദ്യ വിവരണം.
ഈ വികസനം ഉണ്ടായിരുന്നിട്ടും, ലാമിനേറ്റഡ് വെനീറുകൾ ഫർണിച്ചർ വ്യവസായത്തിന് പുറത്ത് വാണിജ്യപരമായ ഉപയോഗങ്ങൾ കണ്ടെത്തുന്നതിന് ഏകദേശം നൂറ് വർഷങ്ങൾ എടുത്തു. ഏകദേശം 1890 ൽ, വാതിലുകൾ നിർമ്മിക്കാൻ ലാമിനേറ്റഡ് വുഡുകൾ ആദ്യമായി ഉപയോഗിച്ചു. ആവശ്യം വർദ്ധിച്ചതോടെ, നിരവധി കമ്പനികൾ വാതിലുകൾക്ക് മാത്രമല്ല, റെയിൽറോഡ് കാറുകൾ, ബസുകൾ, വിമാനങ്ങൾ എന്നിവയിലും ഉപയോഗിക്കുന്നതിന് മൾട്ടിപ്പിൾ-പ്ലൈ ലാമിനേറ്റഡ് വുഡിന്റെ ഷീറ്റുകൾ നിർമ്മിക്കാൻ തുടങ്ങി. ഈ വർദ്ധിച്ച ഉപയോഗം ഉണ്ടായിരുന്നിട്ടും, ചില കരകൗശല വിദഗ്ധർ അവരെ പരിഹാസപൂർവ്വം വിളിച്ചതുപോലെ, "ഒട്ടിച്ച മരങ്ങൾ" ഉപയോഗിക്കുന്ന ആശയം ഉൽപ്പന്നത്തിന് ഒരു നെഗറ്റീവ് ഇമേജ് സൃഷ്ടിച്ചു. ഈ ഇമേജിനെ പ്രതിരോധിക്കാൻ, ലാമിനേറ്റഡ് മര നിർമ്മാതാക്കൾ ഒത്തുചേർന്ന് ഒടുവിൽ പുതിയ മെറ്റീരിയലിനെ വിവരിക്കാൻ "പ്ലൈവുഡ്" എന്ന പദത്തിൽ സ്ഥിരതാമസമാക്കി.
1928-ൽ, ആദ്യത്തെ സ്റ്റാൻഡേർഡ് വലുപ്പത്തിലുള്ള 4 അടി ബൈ 8 അടി (1.2 മീറ്റർ ബൈ 2.4 മീറ്റർ) പ്ലൈവുഡ് ഷീറ്റുകൾ അമേരിക്കയിൽ പൊതു കെട്ടിട നിർമ്മാണ വസ്തുവായി ഉപയോഗിക്കുന്നതിനായി അവതരിപ്പിച്ചു. തുടർന്നുള്ള ദശകങ്ങളിൽ, മെച്ചപ്പെട്ട പശകളും പുതിയ ഉൽപാദന രീതികളും പ്ലൈവുഡിനെ വൈവിധ്യമാർന്ന ആപ്ലിക്കേഷനുകൾക്ക് ഉപയോഗിക്കാൻ അനുവദിച്ചു. ഇന്ന്, പ്ലൈവുഡ് പല നിർമ്മാണ ആവശ്യങ്ങൾക്കും മുറിച്ച തടിക്ക് പകരമായി ഉപയോഗിച്ചു, പ്ലൈവുഡ് നിർമ്മാണം ലോകമെമ്പാടും കോടിക്കണക്കിന് ഡോളർ വിലമതിക്കുന്ന ഒരു വ്യവസായമായി മാറിയിരിക്കുന്നു.
പ്ലൈവുഡിന്റെ പുറം പാളികൾ യഥാക്രമം മുഖം എന്നും പിൻഭാഗം എന്നും അറിയപ്പെടുന്നു. മുഖം എന്നത് ഉപയോഗിക്കേണ്ടതോ കാണേണ്ടതോ ആയ പ്രതലമാണ്, അതേസമയം പിൻഭാഗം ഉപയോഗിക്കാതെയോ മറഞ്ഞിരിക്കുന്നതോ ആയി തുടരുന്നു. മധ്യ പാളി കോർ എന്നറിയപ്പെടുന്നു. അഞ്ചോ അതിലധികമോ പ്ലൈകളുള്ള പ്ലൈവുഡുകളിൽ, ഇന്റർ-മീഡിയറ്റ് പാളികൾ ക്രോസ്ബാൻഡുകൾ എന്നറിയപ്പെടുന്നു.
പ്ലൈവുഡ് ഹാർഡ് വുഡ്സ്, സോഫ്റ്റ് വുഡ്സ്, അല്ലെങ്കിൽ ഇവ രണ്ടും സംയോജിപ്പിച്ച് നിർമ്മിക്കാം. ചില സാധാരണ ഹാർഡ് വുഡുകളിൽ ആഷ്, മേപ്പിൾ, മഹാഗണി, ഓക്ക്, തേക്ക് എന്നിവ ഉൾപ്പെടുന്നു. യുണൈറ്റഡ് സ്റ്റേറ്റ്സിൽ പ്ലൈവുഡ് നിർമ്മിക്കാൻ ഏറ്റവും സാധാരണയായി ഉപയോഗിക്കുന്ന സോഫ്റ്റ് വുഡ് ഡഗ്ലസ് ഫിർ ആണ്, എന്നിരുന്നാലും പൈൻ, ദേവദാരു, സ്പ്രൂസ്, റെഡ് വുഡ് എന്നിവയുടെ നിരവധി ഇനങ്ങൾ ഉപയോഗിക്കുന്നു.
കമ്പോസിറ്റ് പ്ലൈവുഡിന് കണികാബോർഡ് അല്ലെങ്കിൽ അരികുകൾ തമ്മിൽ ബന്ധിപ്പിച്ച ഖര തടി കഷണങ്ങൾ കൊണ്ട് നിർമ്മിച്ച ഒരു കോർ ഉണ്ട്. ഇത് പ്ലൈവുഡ് വെനീർ മുഖവും പിൻഭാഗവും ഉപയോഗിച്ച് പൂർത്തിയാക്കിയിരിക്കുന്നു. വളരെ കട്ടിയുള്ള ഷീറ്റുകൾ ആവശ്യമുള്ളിടത്ത് കമ്പോസിറ്റ് പ്ലൈവുഡ് ഉപയോഗിക്കുന്നു.
തടി പാളികൾ ഒരുമിച്ച് ബന്ധിപ്പിക്കാൻ ഉപയോഗിക്കുന്ന പശയുടെ തരം ഫിനിഷ്ഡ് പ്ലൈവുഡിന്റെ പ്രത്യേക പ്രയോഗത്തെ ആശ്രയിച്ചിരിക്കുന്നു. ഒരു ഘടനയുടെ പുറംഭാഗത്ത് സ്ഥാപിക്കുന്നതിനായി രൂപകൽപ്പന ചെയ്ത സോഫ്റ്റ്വുഡ് പ്ലൈവുഡ് ഷീറ്റുകൾ സാധാരണയായി ഫിനോൾ-ഫോർമാൽഡിഹൈഡ് റെസിൻ പശയായി ഉപയോഗിക്കുന്നു, കാരണം അതിന്റെ മികച്ച ശക്തിയും ഈർപ്പത്തിനെതിരായ പ്രതിരോധവും ഇതിന് കാരണമാകുന്നു. ഒരു ഘടനയുടെ ഉൾഭാഗത്ത് സ്ഥാപിക്കുന്നതിനായി രൂപകൽപ്പന ചെയ്ത സോഫ്റ്റ്വുഡ് പ്ലൈവുഡ് ഷീറ്റുകൾ രക്ത പ്രോട്ടീനോ സോയാബീൻ പ്രോട്ടീൻ പശയോ ഉപയോഗിച്ചേക്കാം, എന്നിരുന്നാലും മിക്ക സോഫ്റ്റ്വുഡ് ഇന്റീരിയർ ഷീറ്റുകളും ഇപ്പോൾ പുറം ഷീറ്റുകൾക്ക് ഉപയോഗിക്കുന്ന അതേ ഫിനോൾ-ഫോർമാൽഡിഹൈഡ് റെസിൻ ഉപയോഗിച്ചാണ് നിർമ്മിച്ചിരിക്കുന്നത്. ഇന്റീരിയർ ആപ്ലിക്കേഷനുകൾക്കും ഫർണിച്ചർ നിർമ്മാണത്തിനും ഉപയോഗിക്കുന്ന ഹാർഡ്വുഡ് പ്ലൈവുഡ് സാധാരണയായി യൂറിയ-ഫോർമാൽഡിഹൈഡ് റെസിൻ ഉപയോഗിച്ചാണ് നിർമ്മിക്കുന്നത്.
ചില പ്രയോഗങ്ങൾക്ക്, പുറംഭാഗത്തിന് ഈർപ്പം, ഉരച്ചിൽ എന്നിവയ്ക്കെതിരെ അധിക പ്രതിരോധം നൽകുന്നതിനോ പെയിന്റ്-ഹോൾഡിംഗ് ഗുണങ്ങൾ മെച്ചപ്പെടുത്തുന്നതിനോ, പ്ലാസ്റ്റിക്, ലോഹം, അല്ലെങ്കിൽ റെസിൻ-ഇംപ്രെഗ്നേറ്റഡ് പേപ്പർ അല്ലെങ്കിൽ തുണികൊണ്ടുള്ള നേർത്ത പാളി മുഖത്തോ പിൻഭാഗത്തോ (അല്ലെങ്കിൽ രണ്ടിലും) ബന്ധിപ്പിച്ചിരിക്കുന്ന പ്ലൈവുഡ് ഷീറ്റുകൾ ആവശ്യമാണ്. അത്തരം പ്ലൈവുഡിനെ ഓവർലേഡ് പ്ലൈവുഡ് എന്ന് വിളിക്കുന്നു, ഇത് സാധാരണയായി നിർമ്മാണം, ഗതാഗതം, കാർഷിക വ്യവസായങ്ങൾ എന്നിവയിൽ ഉപയോഗിക്കുന്നു.
മറ്റ് പ്ലൈവുഡ് ഷീറ്റുകൾ ഉപരിതലത്തിന് ഒരു പൂർണ്ണ രൂപം നൽകുന്നതിന് ഒരു ദ്രാവക സ്റ്റെയിൻ കൊണ്ട് പൂശിയേക്കാം, അല്ലെങ്കിൽ പ്ലൈവുഡിന്റെ ജ്വാല പ്രതിരോധം അല്ലെങ്കിൽ അഴുകൽ പ്രതിരോധം മെച്ചപ്പെടുത്തുന്നതിന് വിവിധ രാസവസ്തുക്കൾ ഉപയോഗിച്ച് ചികിത്സിക്കാം.
പ്ലൈവുഡിന് രണ്ട് വിശാലമായ ക്ലാസുകളുണ്ട്, ഓരോന്നിനും അതിന്റേതായ ഗ്രേഡിംഗ് സംവിധാനമുണ്ട്.
ഒരു ക്ലാസ് നിർമ്മാണവും വ്യാവസായികവും എന്നാണ് അറിയപ്പെടുന്നത്. ഈ ക്ലാസിലെ പ്ലൈവുഡുകൾ പ്രധാനമായും അവയുടെ ശക്തിക്കായി ഉപയോഗിക്കുന്നു, കൂടാതെ അവയുടെ എക്സ്പോഷർ ശേഷിയും മുഖത്തും പിന്നിലും ഉപയോഗിക്കുന്ന വെനീറിന്റെ ഗ്രേഡും അനുസരിച്ചാണ് റേറ്റുചെയ്യുന്നത്. പശയുടെ തരം അനുസരിച്ച് എക്സ്പോഷർ ശേഷി ഇന്റീരിയർ അല്ലെങ്കിൽ എക്സ്റ്റീരിയർ ആകാം. വെനീർ ഗ്രേഡുകൾ N, A, B, C, അല്ലെങ്കിൽ D എന്നിവ ആകാം. N ഗ്രേഡിന് വളരെ കുറച്ച് ഉപരിതല വൈകല്യങ്ങൾ മാത്രമേ ഉള്ളൂ, അതേസമയം D ഗ്രേഡിന് നിരവധി കെട്ടുകളും പിളർപ്പുകളും ഉണ്ടാകാം. ഉദാഹരണത്തിന്, ഒരു വീട്ടിൽ സബ്ഫ്ലോറിംഗിനായി ഉപയോഗിക്കുന്ന പ്ലൈവുഡിന് "ഇന്റീരിയർ CD" എന്ന് റേറ്റുചെയ്തിരിക്കുന്നു. ഇതിനർത്ഥം ഇതിന് D ബാക്ക് ഉള്ള ഒരു C ഫെയ്സ് ഉണ്ട്, കൂടാതെ പശ സംരക്ഷിത സ്ഥലങ്ങളിൽ ഉപയോഗിക്കാൻ അനുയോജ്യമാണ്. എല്ലാ നിർമ്മാണ, വ്യാവസായിക പ്ലൈവുഡിന്റെയും ആന്തരിക പ്ലൈവുകൾ ഗ്രേഡ് C അല്ലെങ്കിൽ D വെനീർ ഉപയോഗിച്ചാണ് നിർമ്മിച്ചിരിക്കുന്നത്, റേറ്റിംഗ് എന്തുതന്നെയായാലും.
മറ്റൊരു തരം പ്ലൈവുഡ് ഹാർഡ് വുഡ് എന്നും അലങ്കാരം എന്നും അറിയപ്പെടുന്നു. ഈ വിഭാഗത്തിലെ പ്ലൈവുഡുകൾ പ്രധാനമായും അവയുടെ രൂപഭംഗി കണക്കിലെടുത്താണ് ഉപയോഗിക്കുന്നത്, കൂടാതെ ഈർപ്പം പ്രതിരോധത്തിന്റെ ക്രമത്തിൽ സാങ്കേതിക (പുറം), തരം I (പുറം), തരം II (ഇന്റീരിയർ), തരം III (ഇന്റീരിയർ) എന്നിങ്ങനെ തരം തിരിച്ചിരിക്കുന്നു. അവയുടെ ഫേസ് വെനീറുകൾ ഫലത്തിൽ വൈകല്യങ്ങളില്ലാത്തവയാണ്.
അളവുകൾ
പ്ലൈവുഡ് ഷീറ്റുകളുടെ കനം 06 ഇഞ്ച് (1.6 മില്ലീമീറ്റർ) മുതൽ 3.0 ഇഞ്ച് (76 മില്ലീമീറ്റർ) വരെയാണ്. ഏറ്റവും സാധാരണമായ കനം 0.25 ഇഞ്ച് (6.4 മില്ലീമീറ്റർ) മുതൽ 0.75 ഇഞ്ച് (19.0 മില്ലീമീറ്റർ) വരെയാണ്. പ്ലൈവുഡ് ഷീറ്റിന്റെ കോർ, ക്രോസ്ബാൻഡുകൾ, മുഖവും പിൻഭാഗവും വ്യത്യസ്ത കട്ടിയുള്ള വെനീറുകൾ കൊണ്ട് നിർമ്മിച്ചതാണെങ്കിലും, ഓരോന്നിന്റെയും കനം മധ്യഭാഗത്ത് സന്തുലിതമായിരിക്കണം. ഉദാഹരണത്തിന്, മുഖവും പിൻഭാഗവും തുല്യ കനം ആയിരിക്കണം. അതുപോലെ മുകളിലും താഴെയുമുള്ള ക്രോസ്ബാൻഡുകൾ തുല്യമായിരിക്കണം.
കെട്ടിട നിർമ്മാണത്തിൽ ഉപയോഗിക്കുന്ന പ്ലൈവുഡ് ഷീറ്റുകളുടെ ഏറ്റവും സാധാരണമായ വലുപ്പം 4 അടി (1.2 മീറ്റർ) വീതിയും 8 അടി (2.4 മീറ്റർ) നീളവുമാണ്. മറ്റ് സാധാരണ വീതികൾ 3 അടി (0.9 മീറ്റർ) ഉം 5 അടി (1.5 മീറ്റർ) ഉം ആണ്. 1 അടി (0.3 മീറ്റർ) ഇൻക്രിമെന്റുകളിൽ നീളം 8 അടി (2.4 മീറ്റർ) മുതൽ 12 അടി (3.6 മീറ്റർ) വരെ വ്യത്യാസപ്പെടുന്നു. ബോട്ട് നിർമ്മാണം പോലുള്ള പ്രത്യേക ആവശ്യങ്ങൾക്ക് വലിയ ഷീറ്റുകൾ ആവശ്യമായി വന്നേക്കാം.
പ്ലൈവുഡ് നിർമ്മിക്കാൻ ഉപയോഗിക്കുന്ന മരങ്ങൾ സാധാരണയായി തടി നിർമ്മിക്കാൻ ഉപയോഗിക്കുന്ന മരങ്ങളെ അപേക്ഷിച്ച് വ്യാസം കുറവാണ്. മിക്ക കേസുകളിലും, പ്ലൈവുഡ് കമ്പനിയുടെ ഉടമസ്ഥതയിലുള്ള സ്ഥലങ്ങളിലാണ് അവ നട്ടുപിടിപ്പിച്ച് വളർത്തിയിരിക്കുന്നത്. മരങ്ങളുടെ വളർച്ച പരമാവധിയാക്കാനും പ്രാണികളിൽ നിന്നോ തീയിൽ നിന്നോ ഉള്ള നാശനഷ്ടങ്ങൾ കുറയ്ക്കാനും ഈ പ്രദേശങ്ങൾ ശ്രദ്ധാപൂർവ്വം കൈകാര്യം ചെയ്യുന്നു.
മരങ്ങൾ സാധാരണ 4 അടി ബൈ 8 അടി (1.2 മീറ്റർ ബൈ 2.4 മീറ്റർ) പ്ലൈവുഡ് ഷീറ്റുകളാക്കി മാറ്റുന്നതിനുള്ള ഒരു സാധാരണ പ്രവർത്തന ക്രമം ഇതാ:
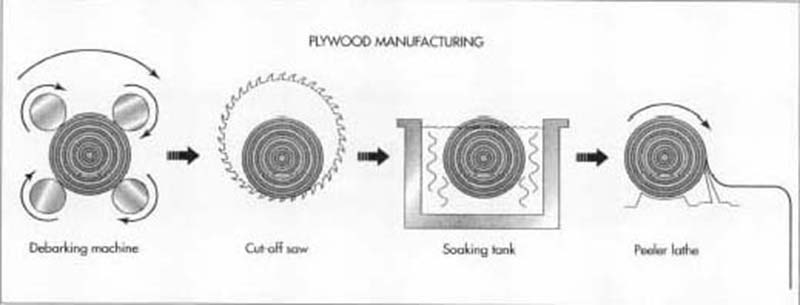
തടികളിൽ നിന്ന് ആദ്യം പുറംതൊലി നീക്കം ചെയ്ത് പീലർ ബ്ലോക്കുകളായി മുറിക്കുന്നു. ബ്ലോക്കുകൾ വെനീർ സ്ട്രിപ്പുകളായി മുറിക്കുന്നതിന്, ആദ്യം അവയെ നനച്ച് തൊലികളഞ്ഞ് സ്ട്രിപ്പുകളായി മുറിക്കുന്നു.
1 ഒരു പ്രദേശത്തെ തിരഞ്ഞെടുത്ത മരങ്ങൾ മുറിക്കാനോ വെട്ടിമാറ്റാനോ തയ്യാറായതായി അടയാളപ്പെടുത്തിയിരിക്കുന്നു. ഗ്യാസോലിൻ ഉപയോഗിച്ച് പ്രവർത്തിക്കുന്ന ചെയിൻ സോകൾ ഉപയോഗിച്ചോ അല്ലെങ്കിൽ ഫെല്ലറുകൾ എന്നറിയപ്പെടുന്ന ചക്ര വാഹനങ്ങളുടെ മുൻവശത്ത് ഘടിപ്പിച്ചിരിക്കുന്ന വലിയ ഹൈഡ്രോളിക് ഷിയറുകൾ ഉപയോഗിച്ചോ മുറിക്കൽ നടത്താം. വീണ മരങ്ങളിൽ നിന്ന് ചെയിൻ സോകൾ ഉപയോഗിച്ച് അവയവങ്ങൾ നീക്കം ചെയ്യുന്നു.
2 വെട്ടിമാറ്റിയ മരക്കൊമ്പുകൾ, അല്ലെങ്കിൽ തടിക്കഷണങ്ങൾ, സ്കിഡറുകൾ എന്നറിയപ്പെടുന്ന ചക്ര വാഹനങ്ങൾ ഉപയോഗിച്ച് ഒരു ലോഡിംഗ് ഏരിയയിലേക്ക് വലിച്ചിടുന്നു. തടിക്കഷണങ്ങൾ നീളത്തിൽ മുറിച്ച് പ്ലൈവുഡ് മില്ലിലേക്കുള്ള യാത്രയ്ക്കായി ട്രക്കുകളിൽ കയറ്റുന്നു, അവിടെ അവ ലോഗ് ഡെക്കുകൾ എന്നറിയപ്പെടുന്ന നീണ്ട കൂമ്പാരങ്ങളിൽ അടുക്കിവയ്ക്കുന്നു.
3 തടികൾ ആവശ്യമുള്ളതിനാൽ, റബ്ബർ ടയർ ചെയ്ത ലോഡറുകൾ ഉപയോഗിച്ച് അവയെ ലോഗ് ഡെക്കുകളിൽ നിന്ന് എടുത്ത് ഡീബാർക്കിംഗ് മെഷീനിലേക്ക് കൊണ്ടുവരുന്ന ഒരു ചെയിൻ കൺവെയറിൽ സ്ഥാപിക്കുന്നു. ഈ യന്ത്രം കൂർത്ത പല്ലുള്ള ഗ്രൈൻഡിംഗ് വീലുകൾ ഉപയോഗിച്ചോ ഉയർന്ന മർദ്ദമുള്ള വെള്ളത്തിന്റെ ജെറ്റുകൾ ഉപയോഗിച്ചോ പുറംതൊലി നീക്കം ചെയ്യുന്നു, അതേസമയം തടി അതിന്റെ നീണ്ട അച്ചുതണ്ടിൽ പതുക്കെ കറങ്ങുന്നു.
പുറംതൊലി നീക്കം ചെയ്ത തടിക്കഷണങ്ങൾ ഒരു ചെയിൻ കൺവെയറിൽ മില്ലിലേക്ക് കൊണ്ടുപോകുന്നു, അവിടെ ഒരു വലിയ വൃത്താകൃതിയിലുള്ള വാൾ അവയെ ഏകദേശം 8 അടി -4 ഇഞ്ച് (2.5 മീ) മുതൽ 8 അടി -6 ഇഞ്ച് (2.6 മീ) വരെ നീളമുള്ള ഭാഗങ്ങളായി മുറിക്കുന്നു, ഇത് സാധാരണ 8 അടി (2.4 മീ) നീളമുള്ള ഷീറ്റുകൾ നിർമ്മിക്കാൻ അനുയോജ്യമാണ്. ഈ തടിക്കഷണങ്ങൾ പീലർ ബ്ലോക്കുകൾ എന്നറിയപ്പെടുന്നു.
5 വെനീർ മുറിക്കുന്നതിന് മുമ്പ്, പീലർ ബ്ലോക്കുകൾ ചൂടാക്കി മുക്കിവയ്ക്കണം, അങ്ങനെ തടി മൃദുവാകും. ബ്ലോക്കുകൾ ആവിയിൽ വേവിക്കുകയോ ചൂടുവെള്ളത്തിൽ മുക്കിവയ്ക്കുകയോ ചെയ്യാം. മരത്തിന്റെ തരം, ബ്ലോക്കിന്റെ വ്യാസം, മറ്റ് ഘടകങ്ങൾ എന്നിവയെ ആശ്രയിച്ച് ഈ പ്രക്രിയയ്ക്ക് 12-40 മണിക്കൂർ എടുക്കും.
6 ചൂടാക്കിയ പീലർ ബ്ലോക്കുകൾ പിന്നീട് പീലർ ലാത്തിലേക്ക് കൊണ്ടുപോകുന്നു, അവിടെ അവ യാന്ത്രികമായി വിന്യസിക്കുകയും ഓരോന്നായി ലാത്തിലേക്ക് നൽകുകയും ചെയ്യുന്നു. ലാത്ത് ബ്ലോക്ക് അതിന്റെ നീളമുള്ള അച്ചുതണ്ടിൽ വേഗത്തിൽ കറങ്ങുമ്പോൾ, ഒരു മുഴുനീള കത്തി ബ്ലേഡ് സ്പിന്നിംഗ് ബ്ലോക്കിന്റെ ഉപരിതലത്തിൽ നിന്ന് 300-800 അടി/മിനിറ്റ് (90-240 മീ/മിനിറ്റ്) എന്ന നിരക്കിൽ തുടർച്ചയായ വെനീർ ഷീറ്റ് അടർത്തിമാറ്റുന്നു. ബ്ലോക്കിന്റെ വ്യാസം ഏകദേശം 3-4 ഇഞ്ച് (230-305 മില്ലിമീറ്റർ) ആയി കുറയ്ക്കുമ്പോൾ, പീലർ കോർ എന്നറിയപ്പെടുന്ന ശേഷിക്കുന്ന മരക്കഷണം ലാത്തിൽ നിന്ന് പുറത്തെടുക്കുകയും ഒരു പുതിയ പീലർ ബ്ലോക്ക് സ്ഥലത്ത് നൽകുകയും ചെയ്യുന്നു.
7 പീലർ ലാത്തിൽ നിന്ന് പുറത്തുവരുന്ന നീളമുള്ള വെനീർ ഷീറ്റ് ഉടനടി പ്രോസസ്സ് ചെയ്യാം, അല്ലെങ്കിൽ അത് നീളമുള്ള, മൾട്ടിപ്പിൾ-ലെവൽ ട്രേകളിൽ സൂക്ഷിക്കാം അല്ലെങ്കിൽ റോളുകളിൽ പൊതിഞ്ഞ് വയ്ക്കാം. എന്തായാലും, അടുത്ത പ്രക്രിയയിൽ വെനീർ ഉപയോഗയോഗ്യമായ വീതിയിലേക്ക് മുറിക്കുന്നത് ഉൾപ്പെടുന്നു, സാധാരണയായി ഏകദേശം 4 അടി (1.2 മീറ്റർ) വീതിയുള്ള പ്ലൈവുഡ് ഷീറ്റുകൾ നിർമ്മിക്കുന്നതിന്. അതേസമയം, ഒപ്റ്റിക്കൽ സ്കാനറുകൾ അസ്വീകാര്യമായ വൈകല്യങ്ങളുള്ള ഭാഗങ്ങൾക്കായി തിരയുന്നു, ഇവ ക്ലിപ്പ് ചെയ്യപ്പെടുകയും, സ്റ്റാൻഡേർഡ് വീതിയിൽ കുറവുള്ള വെനീർ കഷണങ്ങൾ അവശേഷിപ്പിക്കുകയും ചെയ്യുന്നു.
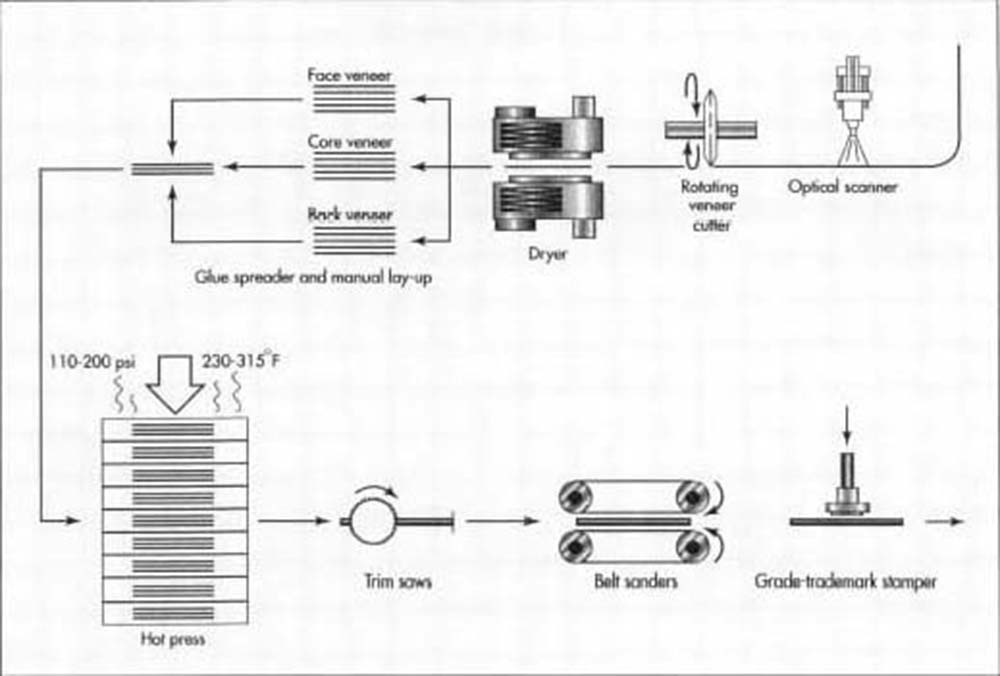
വെനീറിന്റെ നനഞ്ഞ സ്ട്രിപ്പുകൾ ഒരു റോളിലേക്ക് ചുരുട്ടുന്നു, അതേസമയം ഒരു ഒപ്റ്റിക്കൽ സ്കാനർ തടിയിലെ അസ്വീകാര്യമായ ഏതെങ്കിലും തകരാറുകൾ കണ്ടെത്തുന്നു. ഉണങ്ങിയ ശേഷം വെനീർ ഗ്രേഡ് ചെയ്ത് അടുക്കി വയ്ക്കുന്നു. വെനീറിന്റെ തിരഞ്ഞെടുത്ത ഭാഗങ്ങൾ ഒരുമിച്ച് ഒട്ടിക്കുന്നു. ഒരു ചൂടുള്ള പ്രസ്സ് ഉപയോഗിച്ച് വെനീർ ഒരു സോളിഡ് പ്ലൈവുഡ് കഷണമായി അടയ്ക്കുന്നു, അത് ട്രിം ചെയ്ത് മണൽ വാരുന്നതിന് മുമ്പ് അതിന്റെ ഉചിതമായ ഗ്രേഡ് ഉപയോഗിച്ച് സ്റ്റാമ്പ് ചെയ്യും.
8 വെനീറിന്റെ ഭാഗങ്ങൾ ഗ്രേഡ് അനുസരിച്ച് തരംതിരിച്ച് അടുക്കി വയ്ക്കുന്നു. ഇത് സ്വമേധയാ ചെയ്യാം, അല്ലെങ്കിൽ ഒപ്റ്റിക്കൽ സ്കാനറുകൾ ഉപയോഗിച്ച് യാന്ത്രികമായി ചെയ്യാം.
9 അടുക്കിയ ഭാഗങ്ങൾ ഒരു ഡ്രയറിലേക്ക് കയറ്റി അവയുടെ ഈർപ്പം കുറയ്ക്കുകയും അവ ഒരുമിച്ച് ഒട്ടിക്കുന്നതിനുമുമ്പ് ചുരുങ്ങാൻ അനുവദിക്കുകയും ചെയ്യുന്നു. മിക്ക പ്ലൈവുഡ് മില്ലുകളും ഒരു മെക്കാനിക്കൽ ഡ്രയർ ഉപയോഗിക്കുന്നു, അതിൽ കഷണങ്ങൾ ചൂടാക്കിയ അറയിലൂടെ തുടർച്ചയായി നീങ്ങുന്നു. ചില ഡ്രയറുകളിൽ, ഉണക്കൽ പ്രക്രിയ വേഗത്തിലാക്കാൻ ഉയർന്ന വേഗതയിലുള്ള, ചൂടാക്കിയ വായുവിന്റെ ജെറ്റുകൾ കഷണങ്ങളുടെ ഉപരിതലത്തിലൂടെ വീശുന്നു.
10 വെനീറിന്റെ ഭാഗങ്ങൾ ഡ്രയറിൽ നിന്ന് പുറത്തുവരുമ്പോൾ, അവ ഗ്രേഡ് അനുസരിച്ച് അടുക്കി വയ്ക്കുന്നു. വീതി കുറഞ്ഞ ഭാഗങ്ങളിൽ ടേപ്പ് അല്ലെങ്കിൽ പശ ഉപയോഗിച്ച് അധിക വെനീർ സ്പ്ലൈസ് ചെയ്തിരിക്കുന്നു, ഇത് കാഴ്ചയ്ക്കും ശക്തിക്കും പ്രാധാന്യം കുറഞ്ഞ ആന്തരിക പാളികളിൽ ഉപയോഗിക്കാൻ അനുയോജ്യമാക്കുന്നു.
11 ക്രോസ്വേകളിൽ സ്ഥാപിക്കുന്ന വെനീറിന്റെ ഭാഗങ്ങൾ - ത്രീ-പ്ലൈ ഷീറ്റുകളിലെ കോർ, അല്ലെങ്കിൽ അഞ്ച്-പ്ലൈ ഷീറ്റുകളിലെ ക്രോസ്ബാൻഡുകൾ - ഏകദേശം 4 അടി മുതൽ 3 ഇഞ്ച് (1.3 മീറ്റർ) നീളത്തിൽ മുറിച്ചെടുക്കുന്നു.
12 പ്ലൈവുഡിന്റെ ഒരു പ്രത്യേക റണ്ണിനായി വെനീറിന്റെ ഉചിതമായ ഭാഗങ്ങൾ കൂട്ടിച്ചേർക്കുമ്പോൾ, കഷണങ്ങൾ ഒരുമിച്ച് നിരത്തി ഒട്ടിക്കുന്ന പ്രക്രിയ ആരംഭിക്കുന്നു. ഇത് മെഷീനുകൾ ഉപയോഗിച്ച് സ്വമേധയാ അല്ലെങ്കിൽ സെമി-ഓട്ടോമാറ്റിക് ആയി ചെയ്യാം. മൂന്ന്-പ്ലൈ ഷീറ്റുകളുടെ ഏറ്റവും ലളിതമായ സാഹചര്യത്തിൽ, പിൻ വെനീർ പരന്നതായി സ്ഥാപിക്കുകയും ഒരു ഗ്ലൂ സ്പ്രെഡറിലൂടെ കടത്തിവിടുകയും ചെയ്യുന്നു, ഇത് മുകളിലെ പ്രതലത്തിൽ പശയുടെ ഒരു പാളി പ്രയോഗിക്കുന്നു. കോർ വെനീറിന്റെ ചെറിയ ഭാഗങ്ങൾ പിന്നീട് ഒട്ടിച്ച ബാക്കിന് മുകളിൽ ക്രോസ്വേകളായി സ്ഥാപിക്കുകയും മുഴുവൻ ഷീറ്റും ഗ്ലൂ സ്പ്രെഡറിലൂടെ രണ്ടാമതും കടത്തിവിടുകയും ചെയ്യുന്നു. ഒടുവിൽ, ഒട്ടിച്ച കോറിന് മുകളിൽ ഫെയ്സ് വെനീർ സ്ഥാപിക്കുകയും പ്രസ്സിലേക്ക് പോകാൻ കാത്തിരിക്കുന്ന മറ്റ് ഷീറ്റുകൾക്കൊപ്പം ഷീറ്റ് അടുക്കി വയ്ക്കുകയും ചെയ്യുന്നു.
13 ഒട്ടിച്ച ഷീറ്റുകൾ ഒന്നിലധികം തവണ തുറക്കുന്ന ഒരു ഹോട്ട് പ്രസ്സിലേക്ക് ലോഡ് ചെയ്യുന്നു. പ്രസ്സുകൾക്ക് ഒരേസമയം 20-40 ഷീറ്റുകൾ കൈകാര്യം ചെയ്യാൻ കഴിയും, ഓരോ ഷീറ്റും ഒരു പ്രത്യേക സ്ലോട്ടിൽ ലോഡ് ചെയ്യുന്നു. എല്ലാ ഷീറ്റുകളും ലോഡ് ചെയ്യുമ്പോൾ, പ്രസ്സ് അവയെ ഏകദേശം 110-200 psi (7.6-13.8 ബാർ) മർദ്ദത്തിൽ ഒരുമിച്ച് ഞെരുക്കുന്നു, അതേ സമയം അവയെ ഏകദേശം 230-315° F (109.9-157.2° C) താപനിലയിലേക്ക് ചൂടാക്കുന്നു. മർദ്ദം വെനീറിന്റെ പാളികൾക്കിടയിൽ നല്ല സമ്പർക്കം ഉറപ്പാക്കുന്നു, കൂടാതെ ചൂട് പശ പരമാവധി ശക്തിക്കായി ശരിയായി ഉണങ്ങാൻ കാരണമാകുന്നു. 2-7 മിനിറ്റിനുശേഷം, പ്രസ്സ് തുറന്ന് ഷീറ്റുകൾ അൺലോഡ് ചെയ്യുന്നു.
14 പിന്നീട് റഫ് ഷീറ്റുകൾ ഒരു കൂട്ടം സോകളിലൂടെ കടന്നുപോകുന്നു, ഇത് അവയെ അവയുടെ അന്തിമ വീതിയിലും നീളത്തിലും മുറിക്കുന്നു. ഉയർന്ന ഗ്രേഡ് ഷീറ്റുകൾ 4 അടി (1.2 മീറ്റർ) വീതിയുള്ള ബെൽറ്റ് സാൻഡറുകളുടെ ഒരു കൂട്ടത്തിലൂടെ കടന്നുപോകുന്നു, ഇത് മുഖവും പിൻഭാഗവും മണലാക്കുന്നു. പരുക്കൻ പ്രദേശങ്ങൾ വൃത്തിയാക്കാൻ ഇന്റർമീഡിയറ്റ് ഗ്രേഡ് ഷീറ്റുകൾ സ്വമേധയാ സ്പോട്ട് സാൻഡ് ചെയ്യുന്നു. ചില ഷീറ്റുകൾ ഒരു കൂട്ടം വൃത്താകൃതിയിലുള്ള സോ ബ്ലേഡുകളിലൂടെ കടത്തിവിടുന്നു, ഇത് പ്ലൈവുഡിന് ഒരു ടെക്സ്ചർ രൂപം നൽകുന്നതിന് മുഖത്ത് ആഴം കുറഞ്ഞ ചാലുകളെ മുറിക്കുന്നു. അന്തിമ പരിശോധനയ്ക്ക് ശേഷം, ശേഷിക്കുന്ന ഏതെങ്കിലും തകരാറുകൾ പരിഹരിക്കുന്നു.
15 പൂർത്തിയായ ഷീറ്റുകളിൽ ഒരു ഗ്രേഡ്-ട്രേഡ്മാർക്ക് സ്റ്റാമ്പ് ചെയ്തിരിക്കുന്നു, അത് വാങ്ങുന്നയാൾക്ക് എക്സ്പോഷർ റേറ്റിംഗ്, ഗ്രേഡ്, മിൽ നമ്പർ, മറ്റ് ഘടകങ്ങൾ എന്നിവയെക്കുറിച്ചുള്ള വിവരങ്ങൾ നൽകുന്നു. ഒരേ ഗ്രേഡ്-ട്രേഡ്മാർക്ക് ഷീറ്റുകൾ സ്റ്റാക്കുകളിൽ ഒരുമിച്ച് കെട്ടി കയറ്റുമതിക്കായി വെയർഹൗസിലേക്ക് മാറ്റുന്നു.
തടിയുടെ കാര്യത്തിലെന്നപോലെ, പ്ലൈവുഡിന്റെ പൂർണതയുള്ള ഒരു കഷണം എന്നൊന്നില്ല. പ്ലൈവുഡിന്റെ എല്ലാ കഷണങ്ങൾക്കും ഒരു നിശ്ചിത അളവിലുള്ള തകരാറുകൾ ഉണ്ട്. ഈ തകരാറുകളുടെ എണ്ണവും സ്ഥാനവും പ്ലൈവുഡ് ഗ്രേഡ് നിർണ്ണയിക്കുന്നു. നിർമ്മാണ, വ്യാവസായിക പ്ലൈവുഡുകൾക്കുള്ള മാനദണ്ഡങ്ങൾ നാഷണൽ ബ്യൂറോ ഓഫ് സ്റ്റാൻഡേർഡ്സും അമേരിക്കൻ പ്ലൈവുഡ് അസോസിയേഷനും തയ്യാറാക്കിയ ഉൽപ്പന്ന സ്റ്റാൻഡേർഡ് PS1 നിർവചിക്കുന്നു. ഹാർഡ് വുഡ്, അലങ്കാര പ്ലൈവുഡുകൾക്കുള്ള മാനദണ്ഡങ്ങൾ അമേരിക്കൻ നാഷണൽ സ്റ്റാൻഡേർഡ്സ് ഇൻസ്റ്റിറ്റ്യൂട്ടും ഹാർഡ് വുഡ് പ്ലൈവുഡ് മാനുഫാക്ചറേഴ്സ് അസോസിയേഷനും തയ്യാറാക്കിയ ANSIIHPMA HP നിർവചിക്കുന്നു. ഈ മാനദണ്ഡങ്ങൾ പ്ലൈവുഡിനുള്ള ഗ്രേഡിംഗ് സംവിധാനങ്ങൾ സ്ഥാപിക്കുക മാത്രമല്ല, നിർമ്മാണം, പ്രകടനം, ആപ്ലിക്കേഷൻ മാനദണ്ഡങ്ങൾ എന്നിവ വ്യക്തമാക്കുകയും ചെയ്യുന്നു.
പ്ലൈവുഡ് മരങ്ങളെ വളരെ കാര്യക്ഷമമായി ഉപയോഗിക്കുന്നുണ്ടെങ്കിലും - അടിസ്ഥാനപരമായി അവയെ വേർപെടുത്തി കൂടുതൽ ശക്തവും ഉപയോഗപ്രദവുമായ രീതിയിൽ വീണ്ടും ഒരുമിച്ച് ചേർക്കുന്നുണ്ടെങ്കിലും - നിർമ്മാണ പ്രക്രിയയിൽ ഇപ്പോഴും ഗണ്യമായ മാലിന്യങ്ങൾ അന്തർലീനമാണ്. മിക്ക കേസുകളിലും, ഒരു മരത്തിലെ ഉപയോഗയോഗ്യമായ തടിയുടെ ഏകദേശം 50-75% മാത്രമേ പ്ലൈവുഡായി പരിവർത്തനം ചെയ്യപ്പെടുന്നുള്ളൂ. ഈ കണക്ക് മെച്ചപ്പെടുത്തുന്നതിനായി, നിരവധി പുതിയ ഉൽപ്പന്നങ്ങൾ വികസിപ്പിച്ചുകൊണ്ടിരിക്കുന്നു.
ഒരു പുതിയ ഉൽപ്പന്നം ഓറിയന്റഡ് സ്ട്രാൻഡ് ബോർഡ് എന്നറിയപ്പെടുന്നു, ഇത് ലോഗിൽ നിന്ന് ഒരു വെനീർ നീക്കം ചെയ്ത് കോർ ഉപേക്ഷിക്കുന്നതിനുപകരം, മുഴുവൻ ലോഗും ഇഴകളായി കീറിമുറിച്ചാണ് നിർമ്മിക്കുന്നത്. ഇഴകൾ ഒരു പശയുമായി കലർത്തി പാളികളായി കംപ്രസ് ചെയ്യുന്നു, അങ്ങനെ ഗ്രെയിൻ ഒരു ദിശയിലേക്ക് ഓടുന്നു. ഈ കംപ്രസ് ചെയ്ത പാളികൾ പിന്നീട് പ്ലൈവുഡ് പോലെ പരസ്പരം ലംബകോണുകളിൽ ഓറിയന്റഡ് ചെയ്യുകയും പരസ്പരം ബന്ധിപ്പിക്കുകയും ചെയ്യുന്നു. ഓറിയന്റഡ് സ്ട്രാൻഡ് ബോർഡ് പ്ലൈവുഡ് പോലെ ശക്തമാണ്, കൂടാതെ വില അല്പം കുറവാണ്.
പോസ്റ്റ് സമയം: ഓഗസ്റ്റ്-10-2021